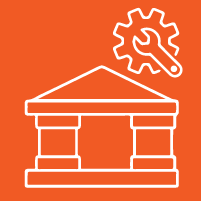
La TPM - Total productive maintenance
Découverte de la TPM
Les objectifs la TPM
Signification de l'acronyme TPM : Total productive maintenance ou maintenance productive totale (en français)
La TPM a pour rôle de maintenir tous les équipements en parfait état de fonctionnement pour éviter les pannes et les retards de processus de fabrication.
Plus globalement, la TPM est un système permettant de maintenir et d'améliorer l'intégrité des systèmes de production, de sécurité et de qualité au moyen d'équipements, de processus et d'employés.
Histoire de la TPM
Seiichi Nakajima a développé la TPM à partir de l’expérience de l’application des meilleures pratiques de maintenance au Japon entre 1950 et 1970. L'une des premières entreprises à en tirer parti était Nippondenso, une entreprise qui a créé des pièces pour Toyota. Ils sont devenus le premier gagnant du prix PM. Un référentiel TPM internationalement reconnu, développé par le JIPM. ( Japan Institute of Plant Management)
Les 8 piliers de la TPM
- Pilier n° 1: amélioration au cas par cas ou élimination des causes de pertes.
- Pilier n° 2: maintenance autonome ou gestion autonome des équipements.
- Pilier n° 3: maintenance planifiée.
- Pilier n°4: amélioration des connaissances et du savoir-faire
- Pilier n° 5: maîtrise de la conception des produits et des équipements.
- Pilier n° 6: maîtrise ou maintenance de la qualité.
- Pilier n° 7: efficacité des services fonctionnels.
- Pilier n° 8: sécurité, conditions de travail et environnement
Les types de maintenance
La maintenance corrective
La maintenance corrective se décompose en deux parties :
- la maintenance curative qui consiste à remplacer les organes défaillants.
- la maintenance palliative est basée sur le fait que l'on ne change pas le dispositif défectueux, mais qu'on le répare.
La maintenance préventive
La maintenance préventive qui se décompose elle-même en trois parties :
- la maintenance systematique qui consiste à changer les pièces d'usures à échéance régulière selon un calendrier déterminée à l'avance. Les consignes sont fixées sur base de l'expérience.
- la maintenance conditionnelle, s'appuie sur des mesures prises sur le terrain et permet d'agir en fonction du dépassement de certains seuils ;
- la maintenance prévisionnelle qui s'appuie à la fois sur la systématique et les mesures en essayant de donner une prévision avec une loi d'usure, si je simplifie.
La maintenance 4.0
La maintenance 4.0 est une maintenance capable de s'adapter. La cyberphysique introduit la notion d'autorégulation du système plutôt que de le gérer. La maintenance 4.0 implique l'adaptation aux spécificités et aux usages de chaque machine. Les programmes de maintenance varient en fonction des mesures et donc des données machine reçues.
La maintenance 4.0 ne remet pas en cause les concepts de maintenance préventive et corrective.
L'apport de la maintenance 4.0 est de fournir davantage d'information sur l'état des machines en temps réel et donc de permettre une maintenance conditionnelle beaucoup plus efficace. L'équilibre dans la maintenance curative et la maintenance prévisionnelle est ainsi réajusté.
Augmenter la disponibilité des machines
L'automaintenance est un enjeu important concernant l'amélioration de la disponibilité des machines. En diminuant les temps d'arrêts (Arrêts programmés et non-programmés), la disponibilité des équipements va augmenter, permettant ainsi de diminuer les délais de production et d'être plus réactif aux changements. En outre, l'automaintenance a l'avantage de permettre la prise en charge immédiatement des micropannes.
Améliorer l'appropriation de la machine par l'opérateur
En mettant en place l'automaintenance, les opérateurs vont avoir une meilleure compréhension du fonctionnement de la machine. C'est un bon moyen pour lutter contre l'effet "boîte noire". Ainsi, l'opérateur sera plus compétent pour détecter les dysfonctionnements et en déterminer les causes.
Améliorer la stabilité du processus
En, s'intéressant à la maintenance de la machine, ce ne sont plus les résultats des problèmes qui sont corrigés, mais les causes. L'automaintenance aura un effet indéniable sur la stabilité du processus. Les opérateurs sont associés aux réflexions permettant de supprimer les pannes.
Diminuer les coûts liés a la maintenance des équipements
L'automaintenance aura un impact important sur la diminution des coûts de maintenance puisque le nombre d'heures de maintenance corrective sera diminué. Le coût des arrêts de fabrication pour maintenance préventive est moins important que celui de la maintenance corrective puisque les arrêts sont planifiés.
Diminuer les risques d'accident
Les risques d'accidents pourront être réduits par une meilleure connaissance des risques liés à la machine.
Présentation de l'automaintenance
Les opérations d'automaintenance
Les opérations d'automaintenance sont :
- Tâche de surveillance
- Surveillance des dégradations (usure et rupture des pièces)
- Surveillance des signaux sonores précurseur à une panne
- Tâche de maintien de la propreté
- Suppression des sources de salissure
- Nettoyage du poste de travail
- Tâche d'entretien
- Lubrification et graissage
- Resserrage des pièces
- Remplacement d'organes simple sur la machine
- Tâche de supervision
- Vérification du carnet de maintenance
- Vérification de la disponibilité des outils de maintenance de premier niveau
- Suivi du nombre de panne (indicateur)
- Analyse des causes
Étapes de mise en application
Préparation
Choisir les équipements.
- Informer les opérateurs.
- Nettoyer les équipements choisis: appliquer les 5S aux équipements concernés.
- Établir les standards de nettoyage
- Établir les contrôles à réaliser
- Établir les gammes de maintenance préventive en fonction
Application
- Former le personnel de production: à la réalisation des opérations prévues dans les gammes de maintenance préventive décidées.
- Établir le planning d’auto-maintenance.
- Réaliser les actions d’auto-maintenance. Valorisation et suivi Contrôler le déroulement de l’application.
Exemple d'application de l'automaintenance
Exemple de tableau de bord d'automaintenance
Voici un exemple de tableau de bord d'automaintenance.
Les indicateurs pourront être :
- Fréquence des pannes (Nombre de panne par jour)
- Nombre d'heures de maintenance de maintenance préventive
- Nombre d'heures de maintenance curative
- Nombre d'arrêts (par machine)
- Audit de l'automaintenance
Les audits d'automaintenance doivent évaluer les points suivants :
- Présence des fiches de maintenance de premier niveau sur les postes.
- Formation des agents de production à l'automaintenance (veiller à la polyvalence)
Découvrez nos micro-formations et conseils en:
- Utilisation des outils qualité
- Le contrôle qualité
- Techniques de résolution de problèmes
- Le tableaux de bord qualité
- ... et bien plus encore!
Formations sur mesure adaptées à VOS besoins, disponibles rapidement.
📩Écrivez-nous à: commentprogresser@gmail.com
Nicolas DEROBERT
