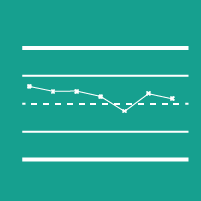
La maîtrise statistique des procédés (SPC / MSP)
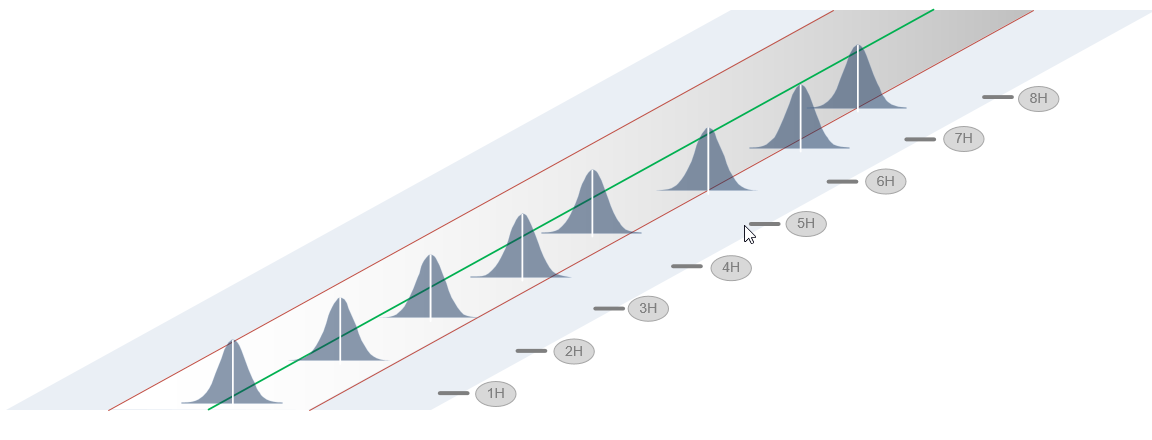
La MSP en questions
Que veut dire MSP/SPC ?
La Maîtrise Statistique de Processus (MSP) est aussi dénommée Statistical Process Control (SPC) en anglais.
De quoi s'agit-il ?
Selon la norme NF X 06-030 la MSP est "un ensemble d'action pour évaluer, régler et maintenir un processus en état de livrer tous ses produits conformes aux spécifications retenues."
Il s'agit d'une démarche déclinée en 2 modes d'action :
Action off-line : Il s'agit d'analyses à froid du processus et des paramètres influents (Analyse avec diagramme Ishikawa, plan-d'experience, analyse de capabilité). Cette typologie d'analyse permet une meilleure sélection des processus et la mise en place d'actions préventives pour rendre les processus plus robustes.
Action on-line : Il s'agit du pilotage des processus par prélèvement d'échantillon et du suivi avec cartes de contrôle.
Pourquoi utiliser la MSP ?
La MSP fait partie des méthodes préventives de gestion de la qualité visant à détecter les dérives plutôt que les défauts. Ainsi, on agit sur les paramètres du processus plutôt que sur sa résultante sur le produit.
Maîtriser la variabilité de processus
La mise en œuvre de la MSP permet de :
- prévenir les effets de déréglage au lieu de faire des constats d'échec a postériori.
- éviter le contrôle à 100%.
- rationaliser les plans d'échantillonnage plutôt que de les choisir par expérience.
Quand utiliser la MSP ?
La méthode MSP n'a pas vocation à être utilisée pour piloter l'ensemble des caractéristiques d'un produit.
Seules les spécifications critiques (importantes
pour le client final et/ou réalisées sur un processus qui a tendance à dériver) seront surveillées.
Spécifications critiques
Un certain nombre d'analyses, telles que l'analyse de la valeur, et l'analyse fonctionnelle, les AMDEC, peuvent être réalisées au préalable.
Ces analyses permettront d'identifier ces caractéristiques.
Mode d'action off-line
Analyse des processus
Il est important de rappeler quelques éléments sur les processus :
- Les facteurs de dispersion (éléments d'entrée) des processus de production varient nécessairement dans le temps. Il est impossible d'avoir deux produits exactement identiques. Ces facteurs de dispersion peuvent être classés selon la logique des 5M .
- Ces variations sont générées par les causes communes (ou causes aléatoires) et les causes spéciales.
- Les variations sur les éléments d'entrée engendrent nécessairement des variations sur les éléments de sortie.
Les éléments de sortie
La plupart des processus produisent des éléments dont les caractéristiques suivent une distribution sous forme de courbe de Gauss. (Voir dossier loi normale )
Ce phénomène est très intéressant pour distinguer les causes communes des causes spéciales.
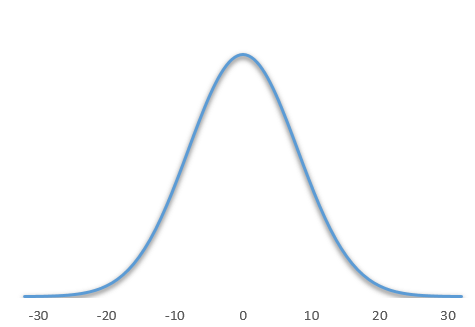
Identifier les causes
Il est nécessaire d'identifier les causes pour pouvoir déterminer les leviers d'action sur lesquels agir.
Pour cela on pourra utiliser des outils tel que :
- le diagramme causes-effet.
- la méthode des 5 pourquoi.
- l'étude de corrélation
- les plans d'expériences
Les facteurs de dispersion
Les facteurs qui influent sur le processus de fabrication ne jamais parfaitement constant. En conséquence, aucun processus de fabrication ne donne des résultats constants. Chaque produit fabriqué est différent.
Les causes communes
Les causes communes (ou causes aléatoires) sont des phénomènes qui influent sur le processus de production, mais qui ont la particularité de ne pas être maîtrisables. "On doit faire avec". La manière dont elles influencent n'est en générale pas clairement établi.
Les causes spéciales
Les causes spéciales (ou cause assignables) sont des causes identifiées dont on connaît le mode d'action et sur lesquelles on peut agir.
Comment agir sur ces causes ?
Réduire au maximum les effets des causes communes
Lorsque la variabilité est uniquement due aux causes communes, on dit que le processus est maîtrisé, stable ou encore sous contrôle.
Identifier et permettre le pilotage des causes spéciales de façon à rendre le processus stable
Pour cela, les causes spéciales doivent être détectées et identifiées. Il faut ensuite les éliminer.
L'analyse de capabilité
L'analyse de la performance du processus à travers l'analyse des capabilités (Cp, Cpk, Pp, Ppk..) est indispensable à la connaissance et la maîtrise des processus : Voir dossier
Mode d'action on-line
Les cartes de contrôle
A chaque fois que c'est possible, il est conseillé d'établir des graphiques concernant les résultats successifs sous forme chronologique mais le terme de graphique de contrôle est toutefois plus adapté surtout lorsqu'ils sont assortis de limites de contrôle.
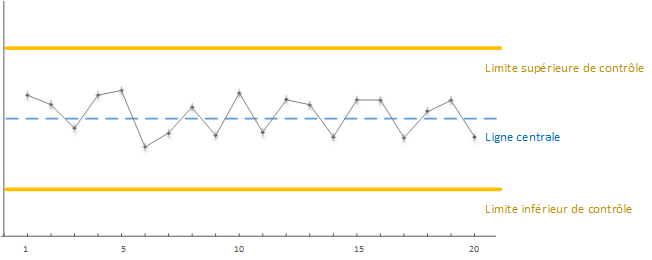
Il s'agit de faire ressortir les variations accidentelles ou inévitables, dues à des causes spéciales ou assignables, des autres variations normales, dues aux causes communes.
Afin de détecter des facteurs de variation de plus en plus fin, les cartes de contrôles sont utilisées.
Attention : Le pilotage par cartes de contrôle ne rendra jamais capable un processus qui ne l'est pas.
Dissection de la carte de contrôle
La carte de contrôle se présente sous forme d'une représentation graphique avec un axe chronologique. Chaque repère indique un numéro d'échantillon.
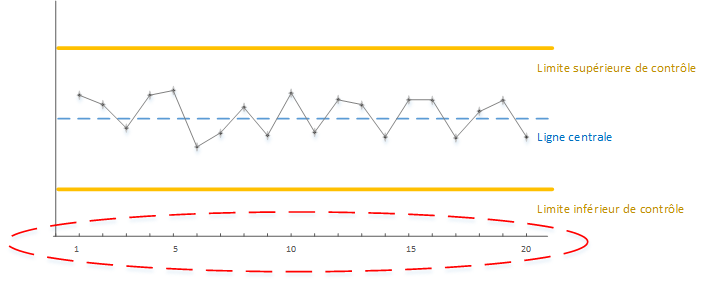
Une ligne centrale représente la moyenne de la statistique suivie.
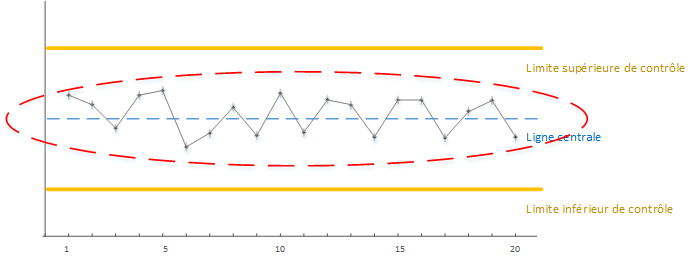
On notera également la présence de 2 limites de contrôle inférieures et supérieures.
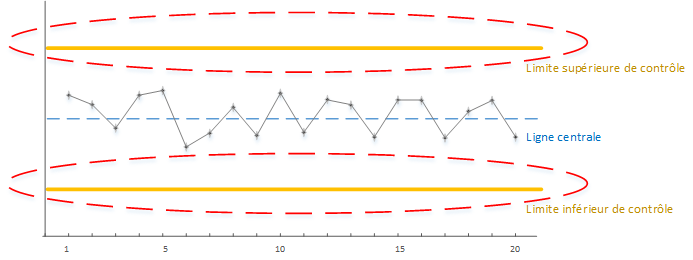
Les limites sont établies de sorte qu'en fonctionnement normal, la quasi-totalité des valeurs tombent à l'intérieur des limites de contrôle. Tant que les points sont à l'intérieur, le processus est jugé stable. Si des points tombent à l'extérieur, cela indique que le processus est non maîtrisé et que des causes spéciales influencent le processus.
Journal de bord du processus
Un journal de bord permet d'enregistrer les événements. Ces événements peuvent être un réglage, une modification des outils...
Ces enregistrements sont utilisés pour identifier et analyser les causes spéciales.
Zones
La carte de contrôle présente différentes zones :
- La zone d'acceptation: processus sous contrôle
- La zone refus: processus hors contrôle
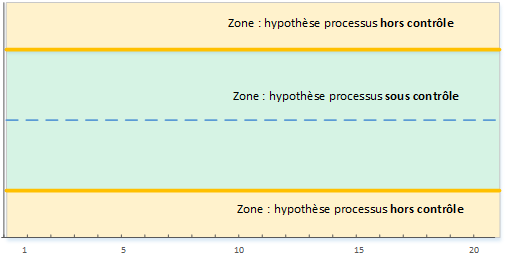
La carte de contrôle peut être considérée comme un ensemble de tests d'hypothèse chronologique. Si le point se situe dans la zone d'acceptation alors on fait l'hypothèse que le processus est sous contrôle.
Si le point est situé hors des limites, alors on rejette l'hypothèse que le processus est sous contrôle.
On parle d'hypothèse car pour la décision se base sur un échantillon et non sur l'ensemble de la population, il existe donc un biais d'échantillonnage .
A partir de là 2 erreurs sont possibles :
L'erreur de première espèce de risque α : On conclut à tort que le processus est hors contrôle. Il s'agit d'une fausse alerte.
L'erreur de deuxième espèce de risque β : On conclut à tort que le processus est sous contrôle. On ne détecte pas un déréglage.
Etapes de construction d'une carte de contrôle
Mise en place
- Choisir un processus à mettre sous-contrôle
- Sélectionner les caractéristiques à mettre sous contrôle
- Choisir le type de contrôle
- Déterminer la fréquence et l'effectif des échantillons
- Calculer les limites de contrôle et de surveillance
Suivi du processus
- Prendre une décision sur l'état du processus
- Identifier les causes spéciales avec le journal de bord
- Mener des actions correctives pour éliminer les causes spéciales et empêcher leur réapparition
Découvrez les cartes de contrôle aux mesures
Découvrez les cartes de contrôle aux attributs
Découvrez nos micro-formations et conseils en:
- Utilisation des outils qualité
- Le contrôle qualité
- Techniques de résolution de problèmes
- Le tableaux de bord qualité
- ... et bien plus encore!
Formations sur mesure adaptées à VOS besoins, disponibles rapidement.
📩Écrivez-nous à: commentprogresser@gmail.com
Nicolas DEROBERT
